Roboguide is the leading of offline programming product on the market for robots and plant simulation. The Roboguide family of process focused software packages allows users to create, program and simulate a robotic workcell in 3-D without the physical need and expense of a prototype workcell setup. With virtual robots and workcell models, of offline programming with Roboguide reduces risk by enabling visualization of single and multi-robot workcell layouts before actual installation. Questions? Contact us today – we’d be happy to speak with you regarding the simulation Software.
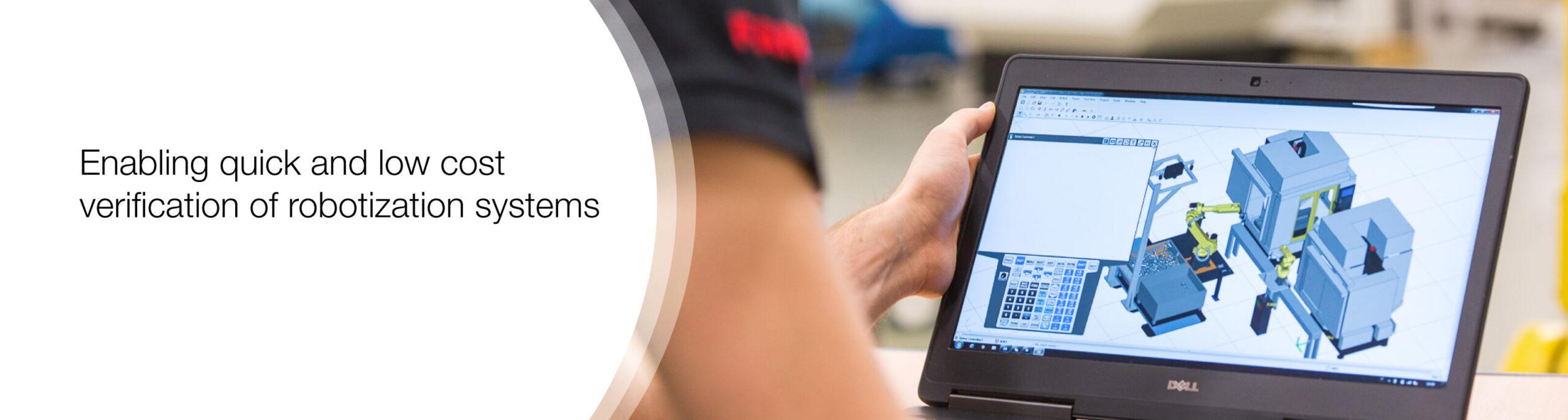
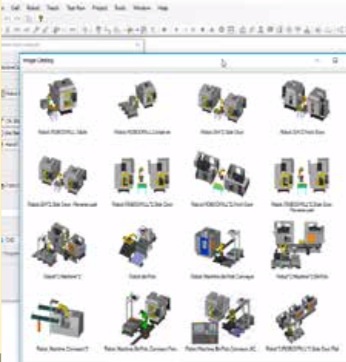
Easy creation of layouts with devices and machines
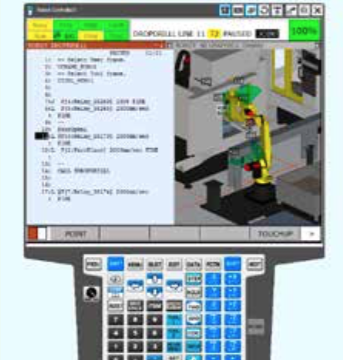
Enhance and debug offline without experiencing downtime or lost production
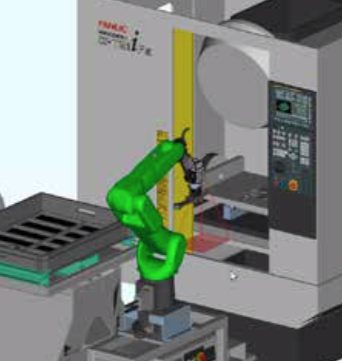
Import of CAD data to give a real look and feel to the application
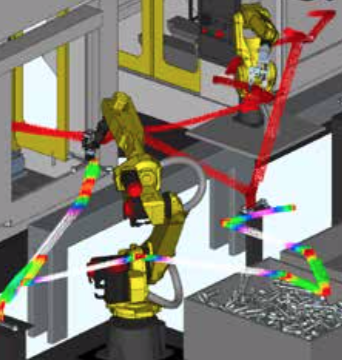
Simple path planning with animation
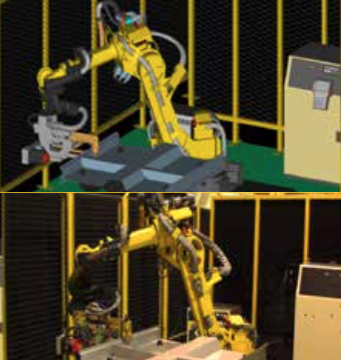
Accurate simulation between the virtual and real world
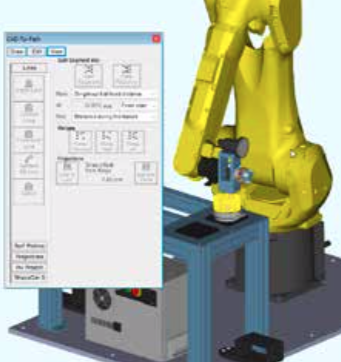
Highly efficient application tools to simplify programming efforts
From design to confirmation
With the on board CAD library you have complete access to all FANUC Robots, Machines and simple tooling. The robot simulation and profiler function contains a full package of process verification details including motion, cycle time validation as well as collision detection and avoidance. It is also available with dedicated tools for specific applications.
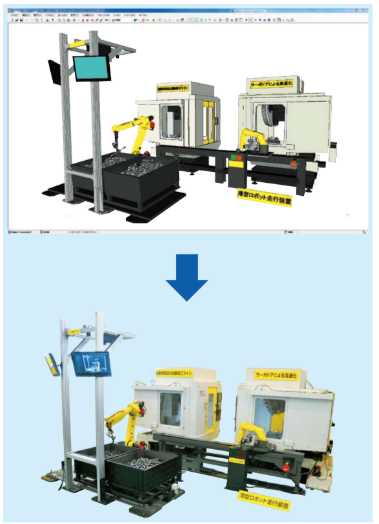
FANUC ROBOGUIDE Simulation Software

HandlingPRO
Simulate and test material handling processes and conduct feasibility studies for robotic applications without the physical need and expense of a prototype work cell setup.
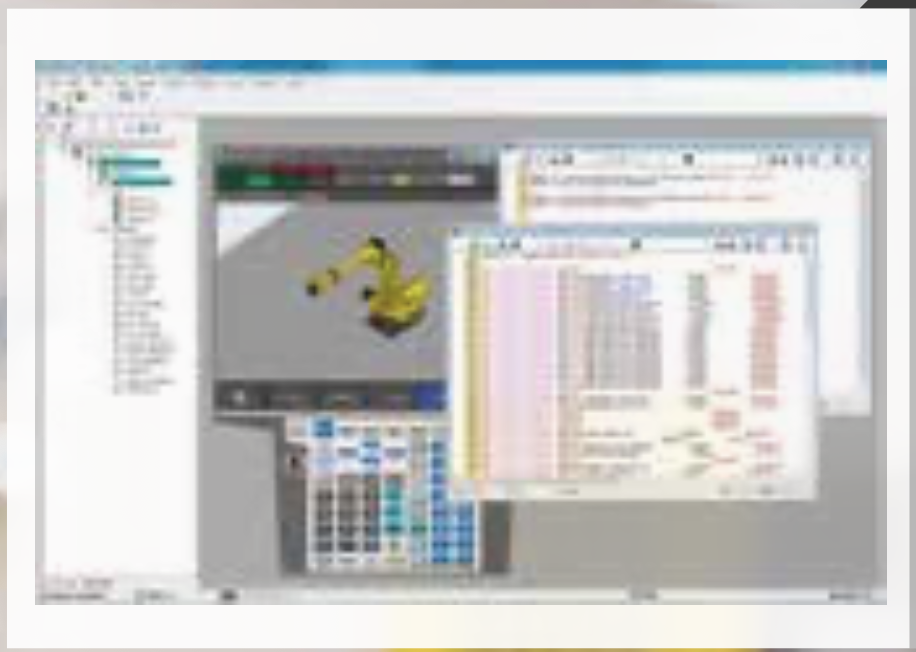
OLPCPRO
Robot program development software that supports the development and maintenance of KAREL and Teach Pendant Programming.
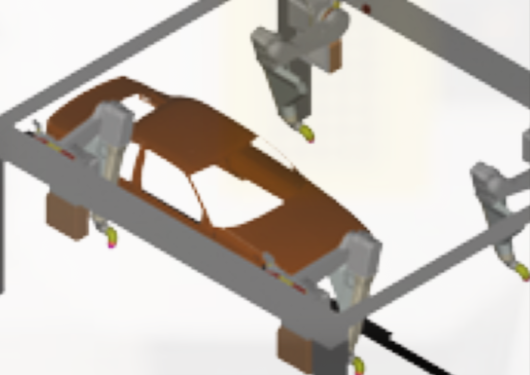
PaintPRO
Graphical offline programming solution that simplifies robotic path teaching and paint process development. It contains special functionality for setting up paint gun displacement, spray size, overlap, paint pattern, paint speed and gun trigger timing.
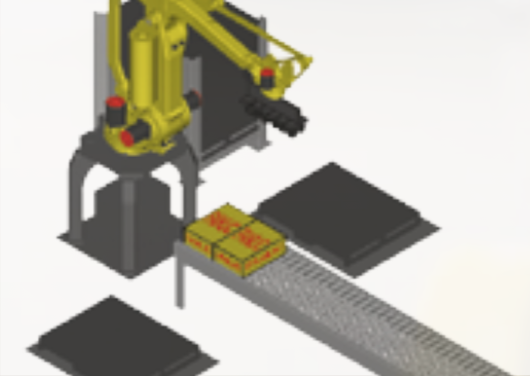
PalletPRO
Can be used to completely build, debug and test a palletizing applications offline. The data created in PalletPRO can then be downloaded to a real robot controller containing the PalletTool software.
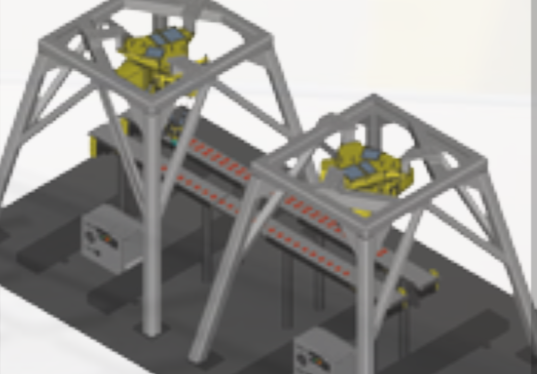
iRPickPRO
FANUC’s latest plug-in to the ROBOGUIDE off-line programming tool allows users to simulate high speed pick and place applications. iRPickPRO can then be downloaded to a real robot controller containing the iRPickPRO software.
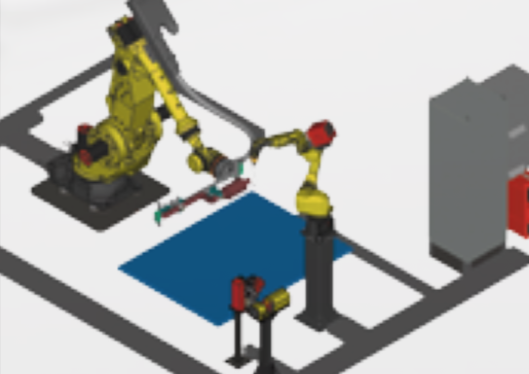
WeldPRO
Simulate a robotic arc welding process in the 3-D world. Driven exclusively by a FANUC Virtual Robot Controller, WeldPRO is empowered with the most accurate program teaching tools and cycle time information available in any simulation package.
FANUC ROBOGUIDE Features
- CAD-to-Path Programming – Easy creation of robot paths from CAD data. A user defines the process requirements on the CAD model, and ROBOGUIDE® automatically generates the robot program.
- The Process Navigator – A fully integrated environment with graphical user interface that guides new and experienced operators quickly through the steps needed to setup and simulate a cell.
- The FANUC robot library – Quick access to any FANUC robot for system layout and simulation. Each robot model comes complete with an associated Virtual Robot Controller and a unique robot solid model to replicate the robot’s operation as precisely as possible within a simulation environment.
- Built-in CAD models – Instant access to many commonly used fixtures, tables, conveyers and end-of-arm tools. Additional simple 3-D geometric shapes are provided as modeling tools to create custom machines, tools and/or fixtures.
- CAD Import (IGES files) – CAD models of existing parts, fixtures and grippers can be imported directly into ROBOGUIDE® to build system layouts and to evaluate system operation.
- Simple robot teaching – Easy creation of robot paths by teaching positions on the part model(s) or by entering robot coordinates manually. An innovative robot programming drag-and-drop Teach ToolTM is combined with a traditional teach pendant style jogging panel.
- Simple robot instructions – Standard teach pendant instructions are supported by ROBOGUIDE® to develop teach pendant programs for throughput verification.
- Robot reach check – A 3-D view of the robot work envelope that helps the user to layout parts, fixtures and other cell components effectively within the work cell.
- Cycle time validation – Calculated, accurate cycle time data is generated by running the taught robot program in simulation mode.
- Collision detection – Visual identification of collisions during robot simulation allows the relocation of the robot, tooling and/or parts before the robot is installed in the plant.
- Profiler – The teach pendant program profiler allows programs to be reviewed quickly for timing bottlenecks and operational slowdowns. Processing problems are solved before the robot is placed into production.
- TP Trace – A unique capability to display the actual robot motion versus the taught path on the teach pendant display. It includes a teach pendant trace by speed, orientation and acceleration, allowing touchup of the robot program before the robot is deployed.